
Visual Management Board Excel Template Kayra Excel
1: SORT OUT - get rid of what's not needed 2: STRAIGHTEN - organize what belongs 3: SCRUB - clean up, see and solve problems 4: SAFETY - make the work area safe 5: STANDARDIZE - assign tasks, track visually 6: SUSTAIN - keep it up (audit and insist) remember. this applies to all areas (value-adding and administrative) basic "6-S" is part.
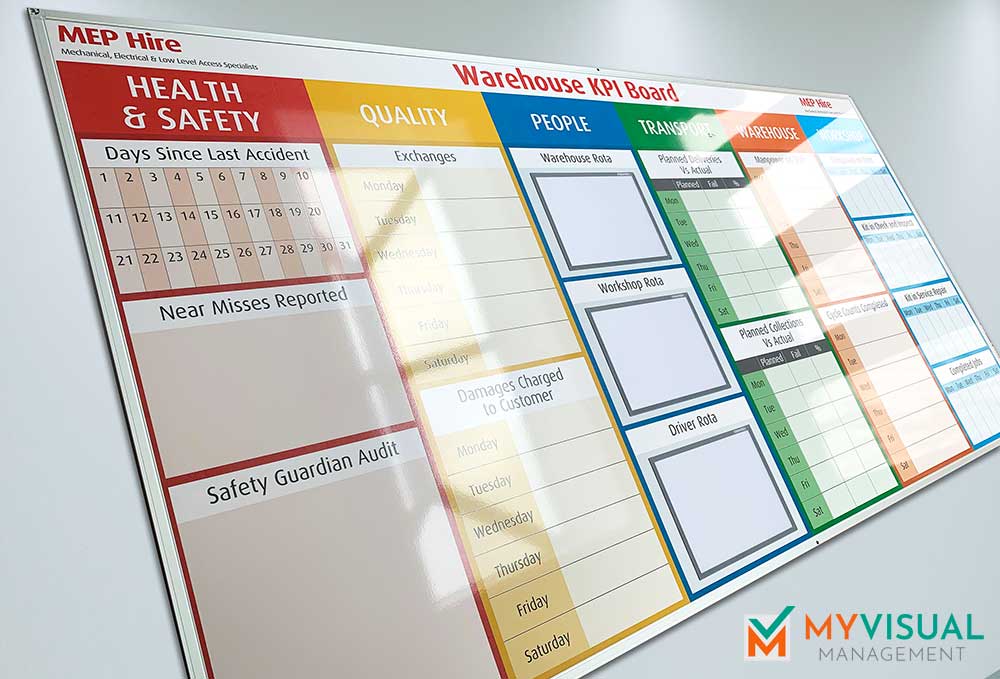
Visual Management Boards Templates
Creating a Visual Management Board TXM Lean Solutions > Blog > Visual Management > Creating a Visual Management Board What is a Visual Management Board? Visual Management Boards provide your team with a means to display and easily communicate the status of key production metrics.
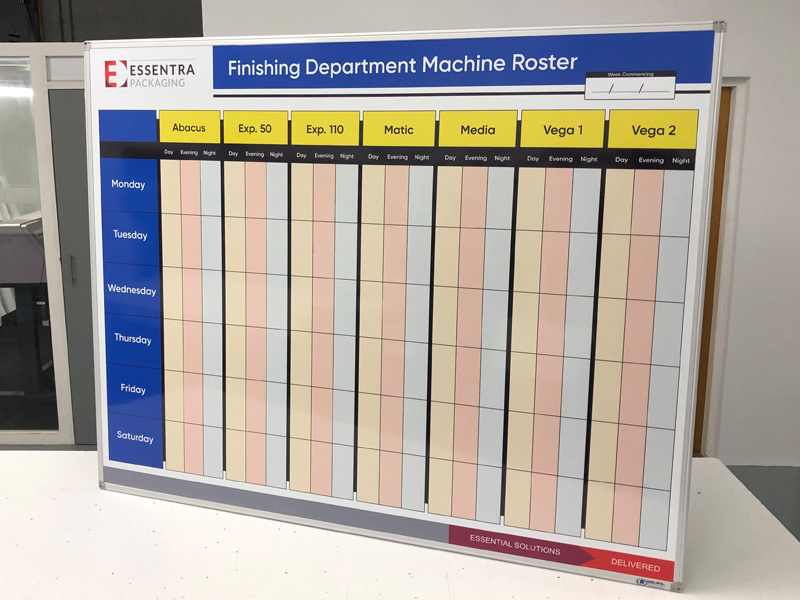
Visual Management Boards Visual Management Solutions
1. The Board Belongs to the Team As a manager, you may have a burning desire to create our own vision of an information centre or visual management board in the middle of your factory or workplace. It is important to resist the temptation. However, A monthly "cross" for quality or safety can replace complex metrics.
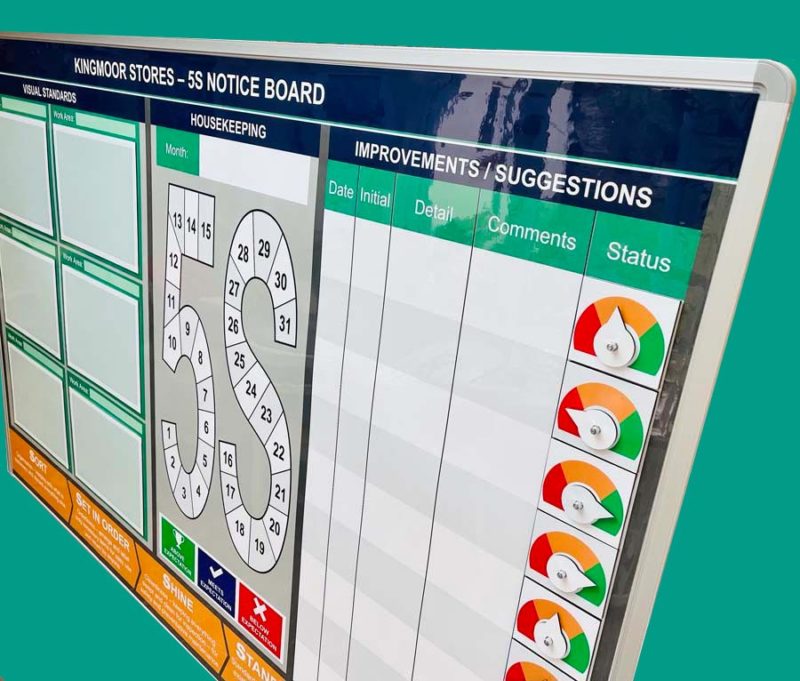
5S Visual Management Boards My Visual Management
Visual management creates an instant view of how processes are performing, can be seen by all, and promotes immediate action. Daily accountability meetings keep everyone informed of the current status of work, pending changes, and provides a forum for public review of action items. Gemba walking keeps leaders in touch with the details of their.

Visual Management Boards (Bespoke) Clarity Visual Management
This board template uses a 3-step approach to product visioning. The end goal is to create a cohesive product vision that encapsulates who your product is for, what it solves, and why your customers should choose it instead of other options. Business Model Canvas
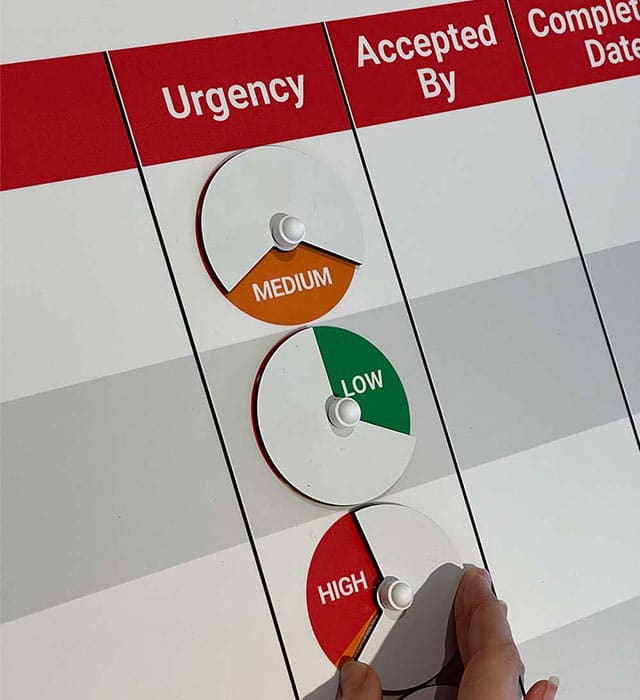
Top tips for visual management boards My Visual Management
Visual management board examples 5 tips for visual management boards How to implement a visual management board using PDSA cycles Health care teams need current performance data to guide their work and sustain improvement. Visual management boards provide teams with at-a-glance information about performance.
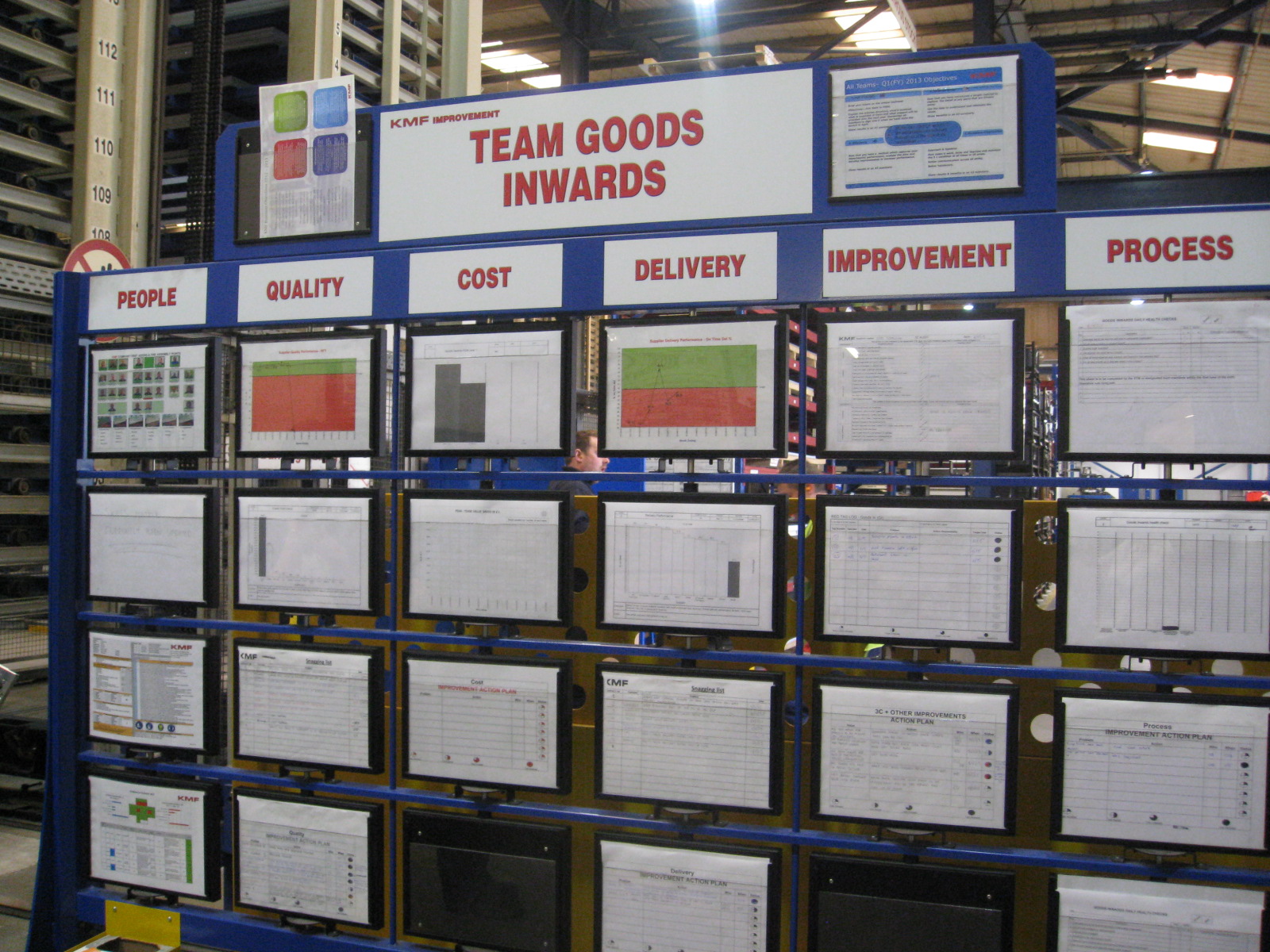
10 ways to make your Visual Management Boards work
A real Visual Management Board should contain three elements: standards, problems, and actions. Standard: In Lean, we set target performance as the standard, rather than average performance. The standards should be clearly indicated on the board, which tells how things should be if everything is perfect. Problem: What is the problem?

What is Visual Management Boards? Visualmitra
Discover how visual management boards work with these visual management board examples. Learn how to use visual management in your workplace

VMT Guide to Visual Management Board Design Pt. 1 VMT
A Kanban board is a visual management tool that is used to manage work in progress (WIP). It is a board that is divided into columns, with each column representing a stage in the workflow. The columns are usually labelled according to the stage in the workflow, such as "To Do," "In Progress," and "Done.".

Visual Management Boards (Bespoke) Clarity Visual Management
Visual management board adalah alat komunikasi yang memberikan informasi sekilas tentang kinerja proses saat ini, baik data kuantitatif maupun kualitatif, untuk membantu staf dan manajer di sebuah divisi mengkoordinasikan dan memandu pekerjaan mereka sehari-hari serta memantau proyek perbaikan yang sedang berlangsung.Visual management board juga dikenal dengan istilah performance board atau.

Visual Management Boards (Bespoke) Clarity Visual Management
Return to Contents. 4. Visual Management Board Example: Elements You Can Use (Figure 1) Image: This image shows an example of a visual management board with numerous elements, such as a list of the patients for the day with safety flags, a table showing observations of surgical checklist use and the outcomes of observation, and measures such as number of days since last harm event.
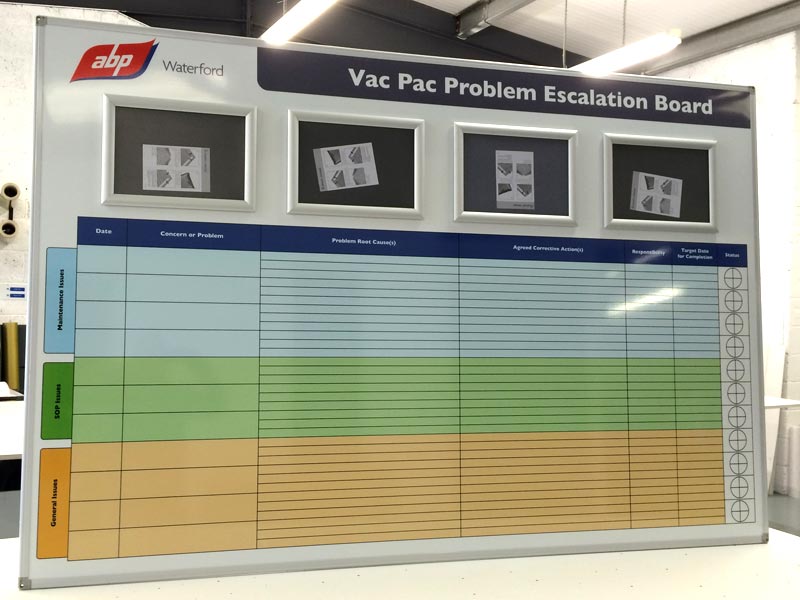
Visual Management Boards Visual Management Solutions
Visual management is most commonly associated with the Kanban boards, and both the Kanban method and the more broad concept of process visualization - "見える化 - Mieruka" in Japanese - had a common origin half a century ago at the Toyota factory floor. Today, Kanban boards are widely used in many industries, including software development, manufacturing, project management, and service.
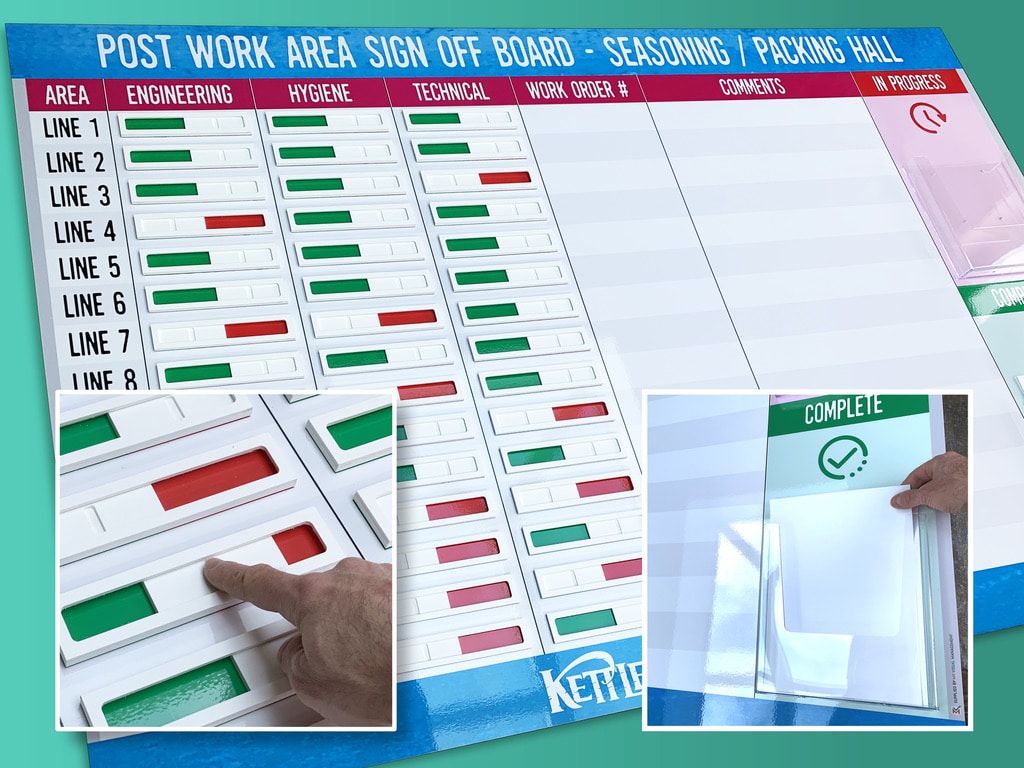
Visual Management board examples My Visual Management
Visual Management Boards: What are They and How Do You Use Them? By Rick Wheeler, Life Cycle Engineering What is visual management? We see it every day, all around us. How do you know when you can safely proceed through an intersection? How do you know how fast you can drive on a stretch of highway?
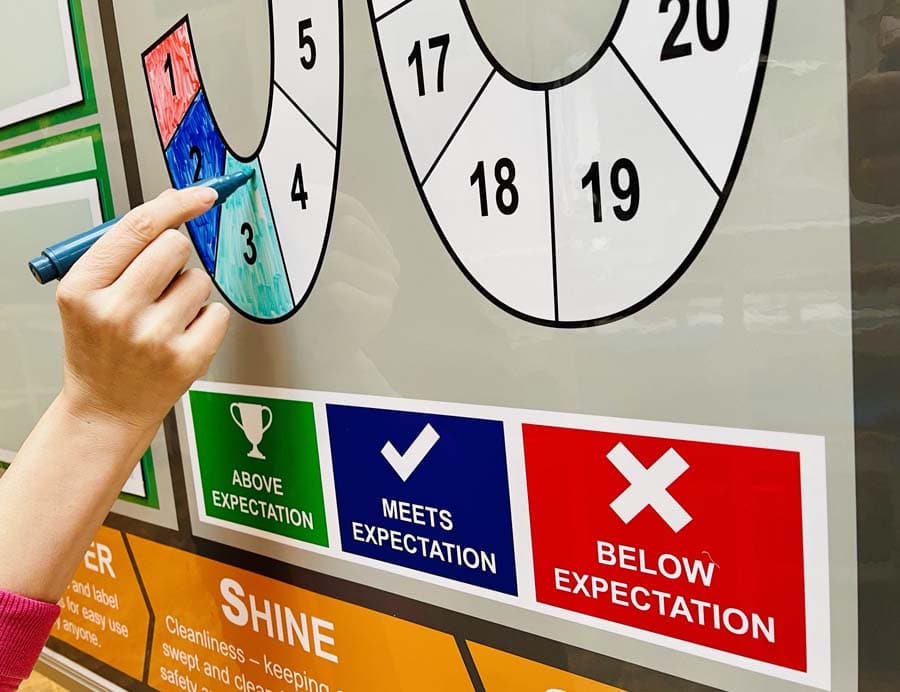
5S Visual Management Boards My Visual Management
In Lean management, Visual Management represents the nervous system. When implementing Lean, visual management is a must-have tool. By visually connecting Lean tools and Lean management Lean management, Visual Management helps to amplify the impact of Lean management. Most businesses have Visual Management Boards, which are one of the most basic Visual Management forms. Some… Read More
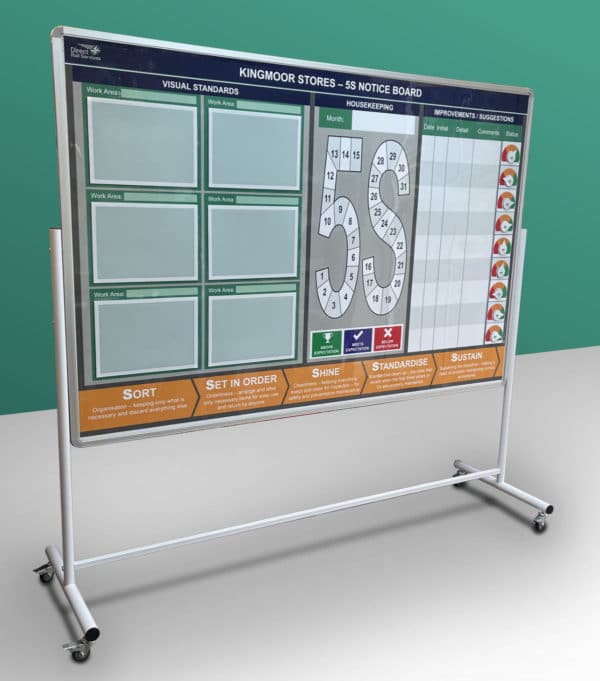
Great example 5S visual performance board My Visual Management
Kanban: Streamlining work processes. In Japanese, "Kanban" translates to a visual sign, and—since the early 2000s—Kanban boards have been playing a pivotal role in simplifying project management. Kanban involves visualizing the workflow on a board, with columns representing different process stages and cards signaling individual tasks. Simultaneously, the Kanban method puts a work-in.

Lean Visual Management Boards in Factories Keep It Simple!
That is why I find the Visual Management Board (VMB) so fascinating. It is a chance for the team to understand work in a new, more accessible way through face to face visual methods. When working with a team that has developed a good VMB, you can see communication walls start the break down as it externalises information for the team to focus on.